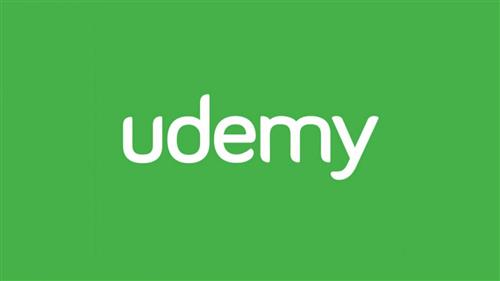
Last updated 5/2023
Created by Sid e-learnings
MP4 | Video: h264, 1280×720 | Audio: AAC, 44.1 KHz, 2 Ch
Genre: eLearning | Language: English + srt | Duration: 16 Lectures ( 3h 4m ) | Size: 1.77 GB
Learn this before you start work in Automotive Industry
What you’ll learn
This Course Aim is to make understand students to have Understanding about CAN & CAN TP
Timeline to learn this course is not so specific because we will keep on add more contents in each protocol
All about protocols that’s been used in different OEM and Supplier for different Vehicles
CAN Protocol & CAN TP
Requirements
No Prerequisite required to learn this course
Description
Table of ContentsIntroduction to Automotive CAN ProtocolOverview of CAN (Controller Area Network)Brief history and development of CAN in the automotive industryAdvantages and limitations of CANCAN Network Architecture and TopologyCAN bus topologyCAN message frame structureCAN data transmissionCAN Protocol LayersPhysical layerData link layerNetwork layerApplication layerCAN Message Formats and ProtocolsStandard CAN messagesExtended CAN messagesJ1939 protocolCANopen protocolOBD-II protocolCAN Bus Diagnostics and TroubleshootingDiagnostic trouble codes (DTCs)Common CAN bus faults and their diagnosisUsing diagnostic tools to troubleshoot CAN systemsCAN Bus Integration with Other Automotive SystemsIntegration of CAN bus with other automotive systems such as engine management, transmission, chassis, and body control systemsUse of CAN bus in modern electric and hybrid vehiclesFuture Trends in Automotive CAN ProtocolEmerging technologies and trends in automotive communication protocolsFuture of CAN in the automotive industrySummary about CAN Protocol and why its important techies to learn this :The CAN (Controller Area Network) protocol is widely used in the automotive industry for communication between different electronic control units (ECUs) in vehicles. CAN was developed by Bosch in the 1980s and has since become a standard in the automotive industry due to its reliability, robustness, and low cost.CAN is used for communication between different automotive systems, such as the engine management system, transmission control system, chassis control system, and body control system. By using a single communication bus, CAN eliminates the need for multiple wiring harnesses and connectors, reducing weight and cost while improving reliability.CAN protocol has two types of messages: standard and extended. The standard CAN message has an 11-bit identifier, while the extended CAN message has a 29-bit identifier. This allows for a greater number of messages to be transmitted on the CAN bus. CAN also uses a priority-based message arbitration system, which ensures that higher priority messages are transmitted first.In addition to the standard CAN protocol, there are also several application-specific protocols used in the automotive industry. For example, the J1939 protocol is commonly used for heavy-duty vehicles, while the CANopen protocol is used in industrial automation and control systems. The OBD-II protocol is used for onboard diagnostics and emissions monitoring in vehicles.One of the key advantages of CAN protocol in the automotive industry is its ability to diagnose faults and malfunctions in the vehicle’s systems. Diagnostic tools can be used to access the CAN bus and retrieve information about the vehicle’s systems and components, including diagnostic trouble codes (DTCs) and real-time data.Overall, CAN protocol has become an essential part of modern automotive technology, enabling efficient and reliable communication between different systems in vehicles.
Who this course is for
For Automotive Engineers and Computer Application Techies[Developers & Testers]
www.udemy.com/course/can-protocol-can-tp/
ddbjp.C.P..C.T.part2.rar.html
ddbjp.C.P..C.T.part1.rar.html
Uploadgig
ddbjp.C.P..C.T.part2.rar
ddbjp.C.P..C.T.part1.rar
NitroFlare
ddbjp.C.P..C.T.part1.rar
ddbjp.C.P..C.T.part2.rar
Leave a Reply
You must be logged in to post a comment.