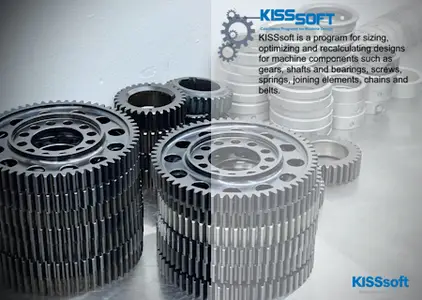
Free Download KISSsoft 2024 SP2 Update | 277.0 mb
Languages Supported: Español, 中文, Deutsch, English,
Français, Italiano, 日本語, Português, Русский
KISSsoft, a part of multi-national Gleason Corporation, is pleased to announce the availability ofKISSsoft 2024 SP2is a modular calculation system for the design, optimization and analysis of machine elements.
Owner:KISSsoft
Product Name:KISSsoft
Version:2024 SP2 Update
Supported Architectures:x64
Website Home Page :www.kisssoft.com
Languages Supported:multilanguage
System Requirements:Windows *
Software Prerequisites:pre-installed KISSsoft 2024 and above
Size:277.0 mb
What’s new in KISSsoft Release 2024
The KISSsoft release 2024 adds the new system module KISSdesign, accelerating the calculation of complex drive trains and replacing the previous KISSsys software. The most important features of the imminent version are:
– System calculation with KISSdesign
– Development environment with SKRIPT
– Additional strength calculations for cylindrical gears
– Newest bevel gear standards ISO 10300 and DIN 3965
– Powerful 3D FEM calculation for tooth root stresses
Once more, KISSsoft and its novelties will give the engineers solutions and tools to size, optimize and rate, ranging from single gears to complete drivetrains. The new functions were developed based on input by current users and they will contribute to the success of your projects.
General
SP 2 – 3D section view
Improvement in the view of the 3D sections in the 3D viewer.
SP 2 – DUI example files extended
The DUI examples files have been extended to use the improved title handling.
SP 2 – Importing projects from previous releases
KISSsoft now supports importing projects from the previous releases 2023 back until 03-2016.
SP 2 – Message added before deleting table data
A message has been added to confirm if the user wants to delete the table data.
SP 2 – Messages with sign @
Messages or other information containing sign @ are now supported.
SP 2 – Overlapping texts in graphic properties removed
Overlapping texts in drop down list in graphic properties have been removed.
SP 2 – Tag fixed for KUI files
Tag fixed for all KUI files.
SP 2 – Units added for length per force
Units mm/N and mm/kN added.
SP 2 – User defined variables created with file load
User defined variables in a calculation file are created directly on load. Therefore they will be available without any user interface.
System Module General
SP 2 – Auxilary results for boundaries attached to loads other than couplings
The generation of auxiliary results is supported when boundaries are attached to loads besides couplings.
SP 2 – Bearing data in tables
Bearing data was swapped in the tables for some cases.
SP 2 – Correction in the view of gear bodies in the 3D viewer
Correction in the view of gear bodies in the 3D viewer, when multiple gear bodies are visible.
SP 2 – External lubrication ID check added
The software now checks if a file refers to an external lubrication ID and in such cases, switches to own input.
SP 2 – Improve runtime of housing calculation
The runtime of the housing calculation is improved.
SP 2 – Improvement in the position of the rings of bearings in the 3D viewer
The outer rings of bearings are now fixed in space and the inner rings follow the supporting shaft in the 3D viewer.
SP 2 – Multiple fixed switchable elements on the same shaft
It is now possible to define multiple fixed switchable elements on the same shaft. The shaft calculation takes care of splitting the power accordingly.
SP 2 – Planet copies in system
The possibility to create planet copies has been removed to simplify user experience.
SP 2 – Planetary efficiency and loss results
Planetary efficiency and loss results are now displayed depending on the defined number of planets.
SP 2 – Progress bar added in the interference check of the 3D viewer
A progress bar is added, showing the progress of calculation during an interference check in the 3D viewer.
SP 2 – Roll, polar and meshing angles
Roll, polar, and meshing angles are now defined when a gear is positioned according to two other fixed gears.
SP 2 – Rolling bearing damage for bearings without rotating speed
Bearing damage is now calculated for still-standing rolling bearings.
SP 2 – Shaft operating temperature in load spectrum
The shaft operating temperature can now be defined for each individual shaft in the system load spectrum.
SP 2 – Show critical element in gear pair safety factors in result overview
The result window now shows the gear pair safety factor for critical elements.
SP 2 – Swap gear geometry
The geometry of two meshing gears can now be swapped on system level via the context menu. This action is only provided when possible.
SP 2 – Switchable elements stiffness and clearance
Stiffness and clearance of Y-axis rotation can now be defined on system level for switchable elements.
Sketcher
SP 2 – Delete key for gear calculation activated
The delete key has been activated for multimesh gear calculations in the sketcher.
Eigenfrequencies
SP 2 – Modal analysis of the system module
Improvement in the positioning of the shafts’ sketch in the modal analysis graphics of the system module,. Eigenmodes characterization is also improved.
Forced Response Gears
SP 2 – Collection of forced response data for the 3D view of the results
The collection of data to be seen in the forced response 3D results has been improved.
SP 2 – Considering of gear mass in forced response based on the definition of "Gear on shaft" in shaft calculation has to be modified
Based on the definition of "Gear on shaft" in shaft calculation, consideration of the gear mass in the forced response is modified to properly model the effect of gear mass in calculating the system response.
SP 2 – General Description in the forced response
Improvement in the handling of documentation point results in the general Description of the forced response.
Gears
SP 2 – Fine sizing center distance of three and four gear trains
Center distance in the fine sizing calculation of three and four gears is automatically taken from the tab "Basic data".
SP 2 – Fine sizing graphic updates on delete
The fine sizing result graphic automatically updates after deleting results from the results table.
SP 2 – Operating backlash calculation
The operating pressure angle is now considered more precisely in the operating backlash calculation.
SP 2 – Root fatigue data for Delrin 51HSE
Root fatigue data is now available for Delrin 51HSE at 20°C, 80°C and 100°C.
Cylindrical Gears Rating
SP 2 – Annex E gear body deformation flank projection
When using gear body influence within the Annex E calculation, the projection for the gap is considered depending on the flank.
SP 2 – Annex E shaft matcher for multimesh in three and four gear chain modules
The shaft matcher is improved during Annex E to better handle multimesh gears in shaft files.
SP 2 – Ensure Annex E results use the correct load bin when shaft and gear have matching load spectrums
When Annex E is run with shaft files that have a matching load spectrum to the gear calculation, each bin is used for the load spectrum results. This also occurs for the contact analysis results.
SP 2 – Import of the hardness curve
The user import of the hardness curve is now improved with an additional stability check.
SP 2 – Optimization of KHβ calculation logic in case of gear body consideration
In case of KHβ calculations including the effect of gear body, the FEM computation is now performed only at the beginning of the iterative calculation, thus reducing a lot the calculation time.
SP 2 – Power calculation for double pinion planetary setup
Power, speed, and torque calculation are now calculated correctly for the double-pinion planetary setup.
Cylindrical Gears Contact Analysis
SP 2 – Contact lines on tooth flank color range
The color range in the "Contact lines on tooth flank" graphic now follows the values specified in the properties.
SP 2 – Export of 3D contact analysis always shows all data
Sometimes, the export of .dat files from 3D contact analysis graphs cut off parts of the data. Export now includes all data shown in graphic.
SP 2 – Improved stability of contact analysis with face chamfers
Contact analysis improved to be more stable in case of heavy face chamfers.
SP 2 – Load contact pattern for internal gears
The no-load contact pattern shows the gap for internal gear meshes.
SP 2 – Saving curves works again for contact analysis graphics
You can now save curves in 2D contact analysis graphics again.
SP 2 – Small overhung edges effect improved on contact analysis results
When running the contact analysis with a small overhung edge, the edge influence has been improved.
Cylindrical Gears Geometry
SP 2 – Calculation of dFf for premanufacturing
The root form diameter dFf for the premanufacturing is now calculated correctly for cases with undercut.
SP 2 – Measurement over the balls for helical asymmetric gears
Calculation of measurement over the balls MdK for helical asymmetric gears improved.
SP 2 – Power skiving check with helix angle defined for the tool
Power skiving check when helix angle is defined for the tool is now calculated more precisely.
SP 2 – Tooth form operation "Manufacture cylindrical gear with a gear generation process"
For tooth form operation "Manufacture cylindrical gear with a gear generation process" where the difference between sP0
* and π/2 is big (Abs(sP0
* – π/2) > 0.25·π), now the user defined sP0
* factor is considered for the calculation of tooth form.
Globoid Worm Gears
SP 2 – Precision of the efficiency calculation
The efficiency calculation for DIN / ISO calculations of the globoid worm gears has been improved to be more precise. Also, the efficiency between the system (s020) module and the z170 module now matches.
SP 2 – Sizing profile shift
The function to size profile shift (SizeProfileShift()) is now available through COM or skript.
Shafts
SP 2 – 3D supports and plain bearings shaft position
The 3D supports and plain bearings position is the center of the object.
SP 2 – 3D synchronizer color matches its icon color
The 3D synchronizer color matches its icon turquoise color.
SP 2 – Improvement in the consideration of the shaft start position, in the 3D viewer of the W010 module
The shaft position in the 3D viewer of the W010 module matches now correctly the "position in global system Y".
SP 2 – Improvement in the rotation animation in the 3D viewer
Improvement in the view of the rotation animation, when a cross section is visible in the 3D viewer.
SP 2 – Improvement in the view of the coordinate system in the 3D viewer
The coordinate system shown in the 3D viewer agrees now with the coordinate system shown in the shaft editor.
SP 2 – Messages in case if the sizing of the required lifetime can’t be executed
Messages are now shown if the sizing of the required lifetime can’t be executed and the limit values for the lifetime is set.
SP 2 – Shaft editor selection with background drawing
The selection of the inner contour has improved when a background drawing is loaded.
SP 2 – The equivalent stresses for static calculation
The equivalent stresses for the neutral line and the bending line outside for the static calculation gave the same results. Now different components are used (case 1: shear stress = 0, case 2: bending stress = 0) to calculate the values.
SP 2 – Thermal expansion of housing in case of housing temperature load spectrum
When calculating shafts with the load spectrum with defined housing temperature this temperature is now considered in the calculation.
SP 2 – Update of gear body in the shaft editor
Improvement of the update of the gear body view in the shaft editor, based on a connected gear calculation.
FEM Calculations
SP 2 – 3D FEM results update after gear material modification
The 3D root stress result updates in case the user changes the material of a gear and performs the
FEM calculation without repeating the LTCA calculation.
SP 2 – Correction in the view of the gear body in the 3D graphic of the gear
The gear body was not shown in the 3D view of the gear after a gear body calculation.
SP 2 – Correction of diameter display in the 3D tooth root stress calculation report
A typo displaying the radius instead of the diameter was corrected in the 3D root stress report.
SP 2 – Equivalent gear diameter of helical gears in 2D FEM tooth root stress calculation
In case of helical gears, the 2D FEM is applied on an equivalent spur gear. After the calculation, all diameters should refer to the original helical gear, not the spur one.
SP 2 – Improvement of 3D root stress sorting algorithm
The sorting algorithm for the calculation and reporting of the 3D tooth root stress was improved and made more robust.
SP 2 – Improvement of the 3D FEM result default display functionality
In cases when a 3D FEM graphic was open and a re-calculation takes place the 3D graphic does not move back to the default state (showing the Principle Stress results). It stays on the result type the user had selected.
SP 2 – Reading the gear body local path when a project is active
The local path definition when working with an active project is now supported. The STEP path of
the gear body can be defined as a global or local path also when a project is active.
SP 2 – Simplification of the export of stiffness matrix of gear body
In case the option to export the stiffness matrix of a gear body has been selected, the export will always overwrite any existing file.
SP 2 – Update of FE meshing library to newest version
Improvement in the FE mesh functionalities mainly coming from an update of the external cm2-library to the new version 5.5.0.
COM-Interface
SP 2 – User interface initialization via COM
The user interface shows the default initialization when called via COM interface.
STEP-Interface
SP 2 – Improvement in the gears exported to a step file from the shaft calculation ““““““““““““Correction of the simplified gear geometry in the step export from the shaft calculation.
CAD-Interfaces
SP 2 – Interface Siemens NX 2406
Interface to Siemens NX 2406 added.
SP 2 – Opening KISSsoft calculation file in CREO
It was not possible to reopen the KISSsoft calculation for Creo 9 and 10.
KISSsys
SP 2 – Color of lines in KISSsys 2D Descriptions
Improvement of the color of lines in the 2D Descriptions of KISSsys.
SP 2 – Forced response calculation
The stability of the forced response calculation has been improved
KISSsoftis a modular calculation program for the design, optimization and verification of machine elements according to international standards. The individually customized software packages for a wide variety of applications guarantee tailor made solutions and the integration to all common CAD software complete the product.
KISSsoft release 2024 highlights
Learn how the enhancements in the KISSsoft 2024 release are useful in your everyday gear calculations.
KISSsoftis part of multi-national Gleason Corporation, as a wholly owned subsidiary. KISSsoft AG directly serves various industries and customers globally. The most powerful source of ideas are our customers: Suggestions and recommendations from innovative companies throughout the world have all contributed to the further development of our software, ensuring that KISSsoft, KISSsys as well as KISSdesign are always at the forefront of technology.
Rapidgator
peeplink.in/a7c35b5249ad
TakeFile
i7241.KISSsoft.2024.SP2.Update.rar.html
Fikper
i7241.KISSsoft.2024.SP2.Update.rar.html
Leave a Reply
You must be logged in to post a comment.