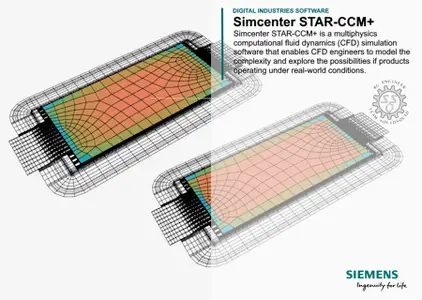
Free Download Siemens STAR-CCM+2406 Build 19.04.007 with Tutorials & Verification Suite | 39.3 Gb
Languages Supported: English, 日本語, 한국어, 中文
TheSiemens Digital Industries Softwaredevelopment team is pleased to announce the availability ofSimcenter Star CCM+ 2406 (19.04.007). With this release we provide engineers across industries with computational fluid dynamics (CFD) capabilities to go faster while modeling the complexity of today’s products. Leverage exciting new features to explore engineering possibilities and turn complexity into a competitive advantage.
Owner:Siemens Digital Industries Software
Product Name:Simcenter Star CCM+
Version:2406 (19.04.007) with Tutorials & Verification Suite *
Supported Architectures:x64
Website Home Page :www.mdx.plm.automation.siemens.com
Languages Supported:multilanguage
System Requirements:Windows & Linux **
Size:39.3 Gb
Siemens.STAR-CCM+2406_19.04.007.R8.Double.Precision.Linux64-SSQ
Siemens.STAR-CCM+2406_19.04.007.R8.Double.Precision.Win64-SSQ
Siemens.STAR-CCM+2406_19.04.007.Single.Precision.Linux64-SSQ
Siemens.STAR-CCM+2406_19.04.007.Single.Precision.Win64-SSQ
Siemens.STAR-CCM+2406_19.04.007_VerificationSuite_&_Tutorials-SSQ
Siemens.STAR-CCM+APT.Series.2406_19.04.007-SSQ
Simcenter STAR-CCM+ 2406 Released. What’s new.
New enhancements in Simcenter STAR-CCM+ are aimed at helping you:
Accurate affordable multiphase simulation including mixtures
Hybrid multiphase is a smart approach for the affordable simulation of liquids in various phases like jets, films, droplets, and mist. However, the current state-of-the-art VOF-Lagrangian Multiphase – Fluid Film approach could not properly cover applications with mixtures (mist), as it needed everything to be resolved or discretely accounted for – which would mean significant computational cost.
To address this, the new release of Simcenter STAR-CCM+ 2406 introduces numerous capabilities to put Mixture Multiphase with Large Scale Interfaces MMP-LSI into the center of hybrid multiphase modeling. Firstly, the new version supports the transition of small Lagrangian droplets to MMP. This enables a more efficient treatment of very small droplets – typically 10s of microns in size, carried with continuous flow – where LMP is not an efficient model. On top, S-Gamma for MMP-LSI allows for the accurate transport and prediction of droplet or bubble size distributions in MMP phases coming from LMP (and other sources). Lastly, LMP Impingement into MMP-LSI Free Surfaces enables you to simulate scenarios where LMP droplets pass into regions of high volume fraction of corresponding continuous phase.
Together these new capabilities allow you to cover applications including mixtures, thereby always leveraging the most efficient multiphase model to be used locally while transitions between the most adequate models will be handled automatically. This innovation enables you to efficiently simulate resolved free surfaces, ballistic droplets, films, and mixtures in a single simulation. The result is accurate predictions of droplet sizes and phase transport, making it efficient for a wide range of applications, like E-motor cooling.
Improved fidelity for battery cell ageing risk assessment
Close
The degradation of a battery cell’s inner active materials leads to long-term decreasing cell performance, posing a challenge to battery designers for identifying mitigation methods.
With the new release of Simcenter STAR-CCM+ 2406, the Sub-grid Particle Surface Film model for cell degradation captures two main ageing mechanisms: Solid-Electrolyte Interphase (SEI) film growth and lithium plating film growth. Designed to be used in conjunction with the 3D cell designer in Simcenter STAR-CCM+ this model allows you to localize cell areas most impacted by ageing, with all models validated against experimental results from the EU Commission-funded project MODALIS.
This innovative approach helps you model the complexity of ageing processes in batteries. It complements long-term time-domain-focused system simulations by providing valuable spatial insights into cell degradation mechanisms and hence contributes to more effective mitigation strategies.
Enhanced particle agglomeration modeling of (wetted) granular flows
Particle granulation is an important part of the process industry and pharmaceutical manufacturing and, plays a crucial role in final drug product quality. Simulation of such industrial processes with solid particle agglomeration or deposition is challenging and requires accurate modeling of the cohesive forces.
With the new release of Simcenter STAR-CCM+ 2406, the Particle Agglomeration model, which replaces the Parallel bonds model, facilitates bond formation based on user-defined local and temporal conditions. This model allows bonds between particles and boundaries and includes bond stiffness independent of mechanical properties. These enhancements enable you to simulate more realistic particle agglomeration processes in various industrial applications, significantly improving realism and reducing computational cost.
Uncompromised contact modeling for complex Fluid-Structure Interaction (FSI) contacts
The standard penalty method for mechanical contacts requires user input for the penalty parameter, which describes contact stiffness. This can be challenging, especially in complex contact situations.
The new release of Simcenter STAR-CCM+ 2406 includes the Augmented Lagrangian Multiplier method (ALM), based on the Uzawa algorithm, which mitigates this by enforcing accurate contact independent of the penalty parameter. It is robust even in sudden contact changes, with an optional automatic update of the penalty parameter for faster convergence. You can now achieve high accuracy and robustness in complex contacts without compromise.
Faster design exploration studies through smart simulation initialization
Close
Extensive design exploration studies benefit from most of the speed-up possibilities to the underlying individual design simulations.
The new release of Simcenter STAR-CCM+ 2406 brings a solution by automatically initializing simulations of a new design closer to expected results, leveraging existing results from the previously simulated nearest neighbor in the design space. That is, the solution takes the calculation result of the solution that is assumed to be the closest. This approach speeds up individual design simulations and consequently reduces the overall design exploration study turnaround time. It should be noted that in cases where the design space and the solution space are correlated in a non-linear way, the time saved may be negligible. For monitoring and understanding purposes, you can easily identify reused designs and designs reusing results with specific Design Sets. The workflow is streamlined with no manual operation required, and this feature is available for Sweep, Design Of Experiment, and Optimization studies, even if you are not saving all Designs.
This simple method enables you to conduct more efficient and faster design exploration processes, significantly enhancing productivity.
Easily evaluate impact of CAD parameters on a cost function
Close
Designing a product often requires analyzing how changes in geometric parameters affect performance, a task that can be daunting without extensive parametric design exploration studies.
In the latest release of Simcenter STAR-CCM+ 2406, you can now compute adjoint sensitivities of a cost function with respect to global parameters used in 3D-CAD, extending the Compute Parameter Sensitivity functionality introduced in version 2306. This enhancement allows you to efficiently evaluate the impact of CAD parameters on global cost functions such as pressure drop, without the need for complex setups. This means you can now quickly understand the effects of design changes on key performance metrics, streamlining the design optimization process. This capability empowers you to make informed decisions faster, reducing the time and effort needed for design iterations.
Enhanced ease-of-use of gradient-based (Adjoint) optimization
Close
Gradient-based adjoint is a powerful optimization method. But it is not always beneficial to calculate and assess the adjoint across the entire geometry. Restricting the computation of sensitivities to specific areas of interest required cumbersome assignment to specific boundaries.
The new release of Simcenter STAR-CCM+ 2406 introduces per-surface subgrouping for the computation of adjoint sensitivities, allowing you to optimize design components more effectively by computing surface sensitivity only where necessary. This setup avoids unnecessary adjoint assessment outside the region of interest, making the gradient-based optimization workflow more efficient and user-friendly.
Immersive results exploration through zero Install Virtual Reality in the web
Utilizing Virtual Reality for CFD simulations previously required a local installation of the Simcenter STAR-CCM+ Virtual Reality. This can be a challenge in highly restrictive IT environments, which can be a reason to not incorporate the technology into novel workflows.
Now, with the new release of Simcenter STAR-CCM+ 2406, Virtual Reality exploration can be triggered from the Simcenter STAR-CCM+ Web Viewer with a single click. This allows you to better understand your results anytime, anywhere, with zero installation. You can easily step into the Scene directly from the browser and seamlessly transition into Virtual Reality, enhancing understanding and sharing insights more effectively.
Higher efficiency in manipulating and defeaturing instanced bodies
Explicitly handling instanced bodies within the embedded 3D-CAD modeler of Simcenter STAR-CCM+ may force you to perform repetitive inefficient geometry preparation steps, whilst also posing the risk of becoming a memory bottleneck.
The resulting challenge of efficiently manipulating instanced bodies is met with the new release of Simcenter STAR-CCM+ 2406 by using pre-existing CAD instance information to create instances of the original body. This approach ensures that modifications applied to any instance can be propagated to all instances, including repair features, sketch commands, and body operations. This results in the reduction of memory consumption proportional to the number of instances within the geometry, making the process more efficient for you.
More efficient boundary layer capturing with Adaptive Mesh Refinement
Close
Adaptive mesh refinement (AMR) offers several benefits amongst which are increased accuracy, improved efficiency, and scalability, as well as reduced memory usage. However, with isotropic refinement of the prism layer, AMR can result in unnecessarily large numbers of cells within the prism layer and the internal domain. This poses an unnecessary penalty on runtime without adding any benefit in terms of increased accuracy or stability.
To address this, the new release of Simcenter STAR-CCM+ 2406 now supports anisotropic refinement of the prism layer during AMR. This refinement strategy reduces the overall number of cells, leading to faster simulation times. You benefit from high flexibility with support for isotropic, tangential, normal, and criterion-based refinement strategies, ensuring more efficient boundary layer capturing with no compromise on accuracy.
Tackle complex rotorcraft simulations with greater ease
Rotorcraft design poses significant challenges due to the complexity of analyzing and predicting flow fields in unsteady trim conditions.
The new trimming option using the blade element method in Simcenter STAR-CCM+ 2406 provides a fast, medium-fidelity solution for analyzing these unsteady flow fields during trimming operations. By incorporating this method, you can streamline the workflow, eliminating the need for manual adjustments after each run, which shortens the overall simulation process. The result is a faster turnaround time compared to the traditional rigid body motion (RBM) approach, allowing you to achieve reliable results quickly. The new release empowers you to tackle complex rotorcraft simulations with greater ease.
Benefit from scalable and faster simulation of rigid body motion
Close
Applications that involve rigid body motion (RBM), such as unsteady vehicle aerodynamics and electric motor cooling, often rely on sliding mesh interfaces, which can be computationally intensive and limit performance on large core counts.
The new Metrics-based intersector in Simcenter STAR-CCM+ 2406 offers a solution to this challenge by providing a faster and more scalable interface intersection calculation.
By employing this innovative interface intersection computation approach, you can achieve enhanced performance and quicker turnaround times for complex simulations involving large interfaces.
Run GPU-accelerated and workflow-supercharged vehicle thermal management simulations
Close
Conjugate Heat Transfer (CHT) applications, such as full Vehicle Thermal Management (VTM), require intensive computations, particularly when radiation models are employed. In such studies, all the solid parts of the vehicle (10k+ in modern setups) must be modeled in detail to ensure no component overheats during a wide range of operating conditions. Surface properties, such as emissivity, of each solid part play a key role in accuracy of the simulations.
Simcenter STAR-CCM+ 2406 introduces a GPU-native Surface to Surface (S2S) radiation model as well as a completely revised workflow to store and input surface properties. The GPU-native S2S model speeds up VTM and other CHT simulations, providing CPU-equivalent solutions by maintaining a unified code base. The new surface property workflow drastically reduces pre-processing time of simulation files featuring thousands of solids via better integration with Material databases and Templates.
By utilizing the power of GPUs and the native automation functionalities, you can achieve significant reductions in the end-to-end simulation process, making it possible to perform detailed thermal analyses more efficiently. These advancements not only accelerates your simulation processes but also ensures that the results are consistent and reliable, regardless of the hardware used.
Leverage more solvers and capabilities ported to GPUs
Close
Furthermore, we ported several solvers and capabilities to GPUs to widen the range of applications that benefit from GPU.
Simcenter STAR-CCM+ 2406 now allows for GPU-native grid sequencing initialization, which speeds up steady-state vehicle aerodynamics. The segregated fluid isothermal and partial slip model transfer to GPUs allows you to run rarified flows more efficiently. Lastly, any type of simulation will benefit from GPU-native derived parts monitoring.
With these enhancements, we continue our strategy of enabling you to run your simulations on the hardware that best fits your business and project needs. We offer a seamless transition between GPUs and CPUs and ensure consistent results through one unified code base.
Choose from more hardware options for GPU-native acceleration
Close
Likewise, we are expanding hardware choices. In Simcenter STAR-CCM+ 2402 release, our first AMD GPU functionality was introduced, to go alongside NVIDIA GPU functionality, with the ability to run on AMD Instinct™ MI200 series GPUs,
With the new release of Simcenter STAR-CCM+ 2406, support has been expanded to include AMD Instinct MI300X and Radeon™ Pro W7x00. This extension provides you with even more flexibility and access to GPU-native acceleration, offering a cost-effective performance boost by supporting both cutting-edge high-performance GPUs and workstation-style graphics cards.
Run an expanded range of applications with SPH
Smoothed-Particle Hydrodynamics (SPH) technology is a powerful alternative method to model complex transient flows with highly dynamic free surface flows. While the introduction of SPH into Simcenter STAR-CCM+ 2402 offers you integrated access to this method alongside the traditional mesh-based approach, the first release was limited in the range of applications. To cover more applications, we are, therefore, continuously expanding SPH capabilities.
With the new release of Simcenter STAR-CCM+ 2406, applications with liquid injections for SPH are now enabled through the support of inlet boundary conditions for SPH particles. This expands the set of applications covered by SPH to include vehicle water runoff and powertrain lubrication with oil jet injection. This increases the versatility of SPH within Simcenter STAR-CCM+ and expands your options to model highly dynamic flows with the most adequate method from within one single simulation environment.
Leverage extended simulation automation intelligence
Implementing Java scripts for automating complex CFD workflows, although powerful and flexible, can be challenging to maintain and update.
In Simcenter STAR-CCM+ 2406 we are expanding the native simulation automation to support multiple physics setups and even more complex workflows within a single simulation. Two new features offer support for turbulence model selection in Stages and nested Simulation Operations sequences. This means you can easily automate RANS-to-DES workflows and robustly initialize aerospace supersonic and hypersonic simulations using a fully automated Inviscid-to-RANS workflow, all with one physics continuum and no need for Java scripting. Nested Simulation operations make it easier to manage, maintain, and troubleshoot complex simulation sequences, enhancing the reliability and efficiency of your workflows. This also allows you to create a single simulation template for multiple scenarios, reducing the need for manual intervention and scripting. These new capabilities help you quickly create and run sophisticated automated workflows, improving productivity, and ensuring consistency across different simulation projects.
These are just a few highlights in Simcenter STAR-CCM+ 2406. Those features will enable you to design better products faster than ever, turning today’s engineering complexity into a competitive advantage.
Simcenter STAR-CCM+is a complete multiphysics solution for the simulation of products and designs operating under real-world conditions. Uniquely, Simcenter STAR-CCM+ brings automated design exploration and optimization to the simulation toolkit of every engineer, allowing you to efficiently explore the entire design space instead of focusing on single point design scenarios.
In 2004 STAR-CCM+ was presented to the public as the first solution able to solve fluid flow and heat transfer problems simultaneously. With the software, flexible license options and Cloud, HPC-enabled uses were introduced, revolutionizing the simulation industry at that time. STAR-CCM+ now encompasses nearly every aspect of Multiphysics modeling and simulation and is the principal CFD solution of Siemens Simcenter portfolio.
Star-CCM+ Tutorial- Overview
This is an overview of the different parts of Star-CCM+ and how to go from starting a file to completion.
Siemens Digital Industries Softwareis a leading global provider of product life cycle management (PLM) software and services with 7 million licensed seats and 71,000 customers worldwide. Headquartered in Plano, Texas, Siemens Digital Industries Software works collaboratively with companies to deliver open solutions that help them turn more ideas into successful products.
Rapidgator
peeplink.in/7a7d61c2c9f7
Fikper
935o7….SETUP.part01.rar.html
935o7….SETUP.part02.rar.html
935o7….SETUP.part03.rar.html
935o7….SETUP.part04.rar.html
935o7….SETUP.part05.rar.html
935o7….SETUP.part06.rar.html
935o7….SETUP.part07.rar.html
935o7….SETUP.part08.rar.html
935o7….SETUP.part09.rar.html
935o7….SETUP.part10.rar.html
Leave a Reply
You must be logged in to post a comment.